What is an Inventory Cycle Count? The Guide for Small Manufacturing Business
We show you how to easily implement the cycle count technique of inventory stocktaking.
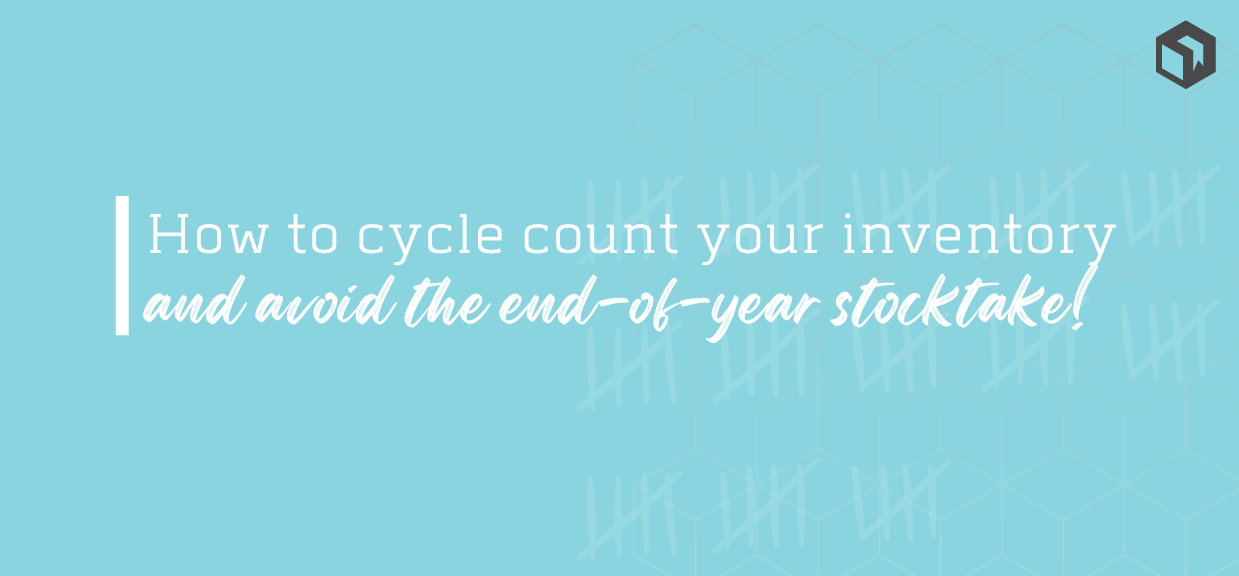
Stock counting is the act of checking each of the materials and products you have on the shelf to ensure that your inventory tallies are correct. This is also known as “stocktaking” or “inventory checking”.
This big, time consuming, usually-at-end-of-year-when-everything-is-already-busy, stock count understandably fills most small businesses with dread and anxiety.
In this article, we are going to show you a much better way by introducing you to the ✨Cycle Count✨. You can use this counting technique to make your stock counting faster, more accurate and far less stress-inducing.
Intrigued? Good! Let’s get started.
Need to get your raw material and product inventory under control?
Try Craftybase - the inventory and manufacturing solution for DTC sellers. Track raw materials and product stock levels (in real time!), lot and batch tracking, COGS, shop floor assignment and much more.
It's your new production central.
Want to jump to a particular section of our cycle count article? We’ve got you covered:
- A short history of stock counting
- What is a Cycle Count?
- How to Implement Cycle Counting: 5 Simple Steps
- When should I cycle count?
- Cycle Count Sampling Methods
- A real-world example of a cycle count process: The Jewelry Maker
- Advantages of implementing cycle counting into your business
- How to handle discrepancies in your stock count
- Inventory Cycle Count Best Practices
- Inventory Cycle Count Software
- Conclusion
A short history of stock counting
In the past, stock counting was typically done once a year in most businesses. This was usually at the end of the financial year when everything else was already busy and stressful. As a result, there were often discrepancies between the current inventory levels and what was recorded in the books.
Stock counting traditionally involves counting each and every item, then comparing the count to the number previously entered in your spreadsheet or inventory system. If the numbers are the same, then all is well and nothing needs to be done. If the numbers are different, then the new number is updated in the books and the stocktaker then promptly moves on to the next one to count. Given small manufacturers have a LOT of material stock on hand at any moment, stock counting your whole inventory in one go is a huge task.
It can take a long time to account for every button, clasp and sq inch of fabric.
For many small self-employed businesses, this means closing their business during the end of year stock count time. This can obviously be a huge burden on any small business and impact on your manufacturing schedules and customer delivery dates.
What if I told you there is an easier way of stock counting that meant that you didn’t have to dedicate huge amounts of time and lose money during the process? That’s where the “Cycle Count” comes in. This counting method allows you to divide your inventory into smaller, more manageable sections and count each section on a rotating basis throughout the year.
Sounds good, right? Let’s explore it further.
What is a Cycle Count?
Let’s also ensure we are all on the same page with the Cycle count inventory definition. A Cycle Count is a way of counting small amounts of your stock throughout the year: spreading out your stocktaking into manageable chunks that can work around the usual day to day operations of your business.
This not only makes stock counting less daunting, but it also ensures that your inventory records are more accurate and up-to-date.
Think of it like regularly checking the oil level in your car rather than waiting for a full service to catch any issues. By counting smaller portions of inventory at a time, you can quickly identify any discrepancies and address them promptly, rather than letting them build up and become overwhelming.
Another benefit of cycle counting is that it can be easily scaled as your business grows. As you add more products to your inventory, you can simply increase the frequency or scope of your cycle counts. Plus, with regular and consistent checks, you can catch any issues before they impact your production process or customer orders.
How to Implement Cycle Counting: 5 Simple Steps
-
Categorize your inventory: Before you start implementing cycle counting, it’s important to first categorize your inventory based on factors such as value, demand, and criticality. This will help you determine which items need to be counted more frequently than others.
-
Determine cycle count frequency: Based on the categories you’ve identified, determine how often each category should be counted. High-value and high-demand items may need to be counted more frequently, while lower-value or less critical items may only need to be counted once a year.
-
Create a schedule: Once you’ve determined the frequency for each category, create a cycle count schedule that outlines when each category will be counted throughout the year.
-
Train your employees: Make sure your employees are trained on the cycle count process and understand the importance of keeping accurate inventory records. This will help ensure that the cycle count process runs smoothly and efficiently.
-
Monitor and adjust: Regularly monitor your inventory levels and compare them to your records to identify any discrepancies. If you notice any issues, adjust your cycle count schedule or frequency as needed to maintain accurate inventory records. This will help you identify any recurring issues and make necessary adjustments to your processes.
When should I cycle count?
How often you choose to cycle count is completely up to you: in large scale manufacturing it is typical to do daily counts, however for smaller operations it may be a case of bi-weekly or even monthly.
The only requirement is to be regular enough to reliably cover most of the materials you work with during the year. Ultimately, the goal is to keep your inventory records as accurate and up-to-date as possible, in a way that fits with your specific business needs and operations.
One important thing to note is that no physical inventory movements should happen during the cycle count window - this means orders should not be packed, stock should not be transferred and materials should not be booked in. This requirement should be clearly signposted to all shop floor teams before the count begins.
Cycle Count Sampling Methods
The sample you select for your cycle count could be a completely random set of materials, or you might like to prioritise materials with high usage / cost.
Alternatively, physical locations may work best if you have your stock arranged in an orderly way - you could work from top to bottom of your storage cabinet, for example. Consider implementing BIN numbers to track your physical stock locations to create more consistency and order to your inventory.
Whichever selection method you choose, the goal is to work regularly through small groupings of your entire stock during the year so that a big one-off count is not necessary at end of year.
There are three main methods you can use to select your samples: Random, Control Group and ABC Analysis.
Control Group Cycle Counts
This method is mainly used when first starting out with Cycle Counting and is typically abandoned in favor of one of the other two methods when the control group has been fully counted and tested.
This method involves selecting a specific group of materials to count - this “control group” should be deliberately selected as a cross section of your total inventory.
You’ll want to keep doing the count at a specified interval until you have a good level of accuracy. The main goal of this approach is to find any issues with the counting and auditing techniques so that they can be improved before cycle counting begins in earnest.
Random Sampling Cycle Counts
This, as its name implies, is done by selecting a group of your materials completely at random. There are two main sub-methods for the random approach, called Constant Population Counting and Diminished Population Counting.
Constant Population Counting is where you select a completely random sample each time, regardless of what has previously been counted. The disadvantage to this approach is that you’ll be sometimes counting the same materials more than once in a period and others may be missed for a significant period of time. It is however the easiest technique to use as you can just randomly take materials from your shelves to count without keeping records of prior counts.
Diminished Population Counting is an improvement on the Constant count technique - as soon as a material has been counted, it is then excluded from future counts until all items have been counted. For this technique, you’ll need to keep records of your counts to ensure you are aware of which ones you have already counted.
ABC Cycle Counting
ABC is the most technical of the approaches to cycle counting as it involves categorising your materials into the groups: A, B and C.
The groups are determined by how often they are used in your production processes and are calculated using the Pareto principle. This principle essentially states that about 80% of the effects come from 20% of the causes - in inventory management this translates into a theory that 80% of your manufacturing involves only 20% of your material parts. Therefore, this approach ensures that you focus on this 20% in your cycle counting, with the other 80% being counted less intensively.
Your “A” items should be the materials that are involved in 80% of your manufactures. “B” items are then 30% of your material inventory which will account for 15% of your manufactures. “C” items are then 50% of your material inventory and 5% of your total manufactures.
Before you can begin using this cycle count approach, every material in your inventory will need to be identified as a A,B or C. Once assigned a category, the number of times that this category needs to be counted needs to be determined - for example, you might choose to count your A materials once a week, your B materials each month and your C materials each quarter.
This approach can have a couple of disadvantages - depending on your C cycle period, these materials may be counted very infrequently which can lead to inaccuracies with your inventory. If your particular manufacturing process doesn’t resemble the pareto rule above (i.e. customised products, OOAK) then you will find it difficult to calculate categories and assign cycle count schedules - in this case, it may be better to use the randomised process detailed above instead.
A real-world example of a cycle count process: The Jewelry Maker
As an example of an inventory cycle count procedures sample, let’s use jewelry maker named Sara who has decided to implement cycle counting in her small manufacturing business. Sara has a diverse inventory of precious gems, metals, and findings. Due to the high value of her materials and the custom nature of her pieces, she opts for the ABC Cycle Counting method.
Sara identifies her ‘A’ items as her most frequently used materials: gold chains, diamond accents, and silver clasps. These materials are involved in about 80% of her creations. Her ‘B’ items include semi-precious stones and bronze settings, while her ‘C’ items are the less frequently used materials, such as enamel accents and copper wire.
Once Sara has categorized her inventory, she determines a schedule for her cycle counts. She decides to count her ‘A’ items weekly, her ‘B’ items monthly, and her ‘C’ items quarterly. This way, her most valuable and frequently used items are constantly monitored, while her less-used items are still accounted for on a regular basis.
Utilizing a cycle count process, Sara was able to significantly improve the accuracy of her inventory records, minimize discrepancies, and streamline her manufacturing process. The result? More time to focus on what she loves most - designing and crafting beautiful jewelry.
Advantages of implementing cycle counting into your business
Inventory accuracy is the backbone of any successful business operation, particularly for manufacturers. It ensures that you have a clear understanding of the materials available at your disposal for production, and aids in making accurate predictions for future business operations. Furthermore, accuracy in inventory enables the efficient fulfillment of customer orders, thereby enhancing customer satisfaction and brand reputation.
Inventory accuracy also contributes significantly to financial stability. Without accurate inventory records, you may face challenges in accounting practices, potentially leading to discrepancies in financial reports and balance sheets. This could result in financial losses or even legal complications in some cases.
Lastly, inventory accuracy is instrumental in preventing overstocking or understocking. Overstocking ties up capital, occupies space, and risks potential wastage of materials. On the other hand, understocking can disrupt production schedules and lead to missed sales opportunities. Hence, maintaining accurate inventory records through practices like cycle counting is not only a best practice but a necessity for businesses to thrive and grow.
How to handle discrepancies in your stock count
So what do you do if you find from one of your cycle counts that your actual count is different to the stock level being calculated in your inventory system? Firstly, don’t panic! Slight differences are a completely normal and expected part of perpetual inventory tracking, especially when running businesses that manufacture products. Treat any difference you find as a way of learning more about your manufacturing and costing process: the more you learn about the way you work and the materials you use, the more opportunity you have to improve your processes and products…and therefore your bottom line.
So, where do we start once we have found a discrepancy? You’ll firstly need to figure out if your numbers are more or less than the actual count as this will often point you in the right direction of the cause.
If your numbers in Craftybase are showing a number higher than your actual count, then you’ll be looking for reasons why you are missing stock. If your numbers are lower in Craftybase, then you’ll be wanting to find out how you have ended up with more stock.
Less stock on hand could mean:
- Your manufacture amounts are being underestimated
- Actual amounts provided by vendors could be less than listed on purchase orders
- You have a “hidden process” that results in loss or wastage
- You have more loss in damaged materials than you are currently aware of
More stock on hand could mean:
- Your manufactures amounts are overestimated
- Actual amounts provided by vendors could be more than listed on purchase orders
- Materials attributed to scrap in one manufacture are being re-used an returned to the system.
A good idea is to write up a quick list of reasons for your particular situation so that you know what you should be looking out for.
Remeasure and recalibrate
If you suspect your counts are out due to your manufactures being over- or under-estimated, you’ll be wanting to pay a little more attention to the measurements on your next couple of manufactures and then comparing these to your current recipe (or past manufactures, if you aren’t using recipes). This reason is often one of the most common, especially for those starting out with this form of inventory tracking.
An important thing to note here: unless your product changes substantially each time you create it, you won’t be needing to measure each time, you’ll only be wanting to do this only when its clear that your estimates are out by a good margin.
Once you have recalibrated, it’s often a good idea at this point to also spend a little time reassessing your pricing to ensure that you are still making your desired margins given your material costings will change based on your new found knowledge about your production process.
Is your Vendor shortchanging you?
If you suspect the difference may be due to certain vendors providing more or less than the agreed amount then it’s wise to start doing some quick mini counts when you receive your next shipments and log them into inventory.
When a difference is discovered, you can either add in a manual adjustment or amend the actual amount received on the expense itself.
Some types of materials will always suffer from miscount and inaccuracy where it’s not always possible to guarantee delivering an exact amount to the customer: beads and buttons are good examples of this.
However, depending on the type of material, you may decide to take this up with the vendor to see if they can start providing more accurate amounts to you in future: not only so that you can better rely on this part of your process for your quantities on hand, but also so that you can ensure that your own margins are not affected by any shortchanging that may be occurring.
Watch out for hidden processes
A good example of a hidden process that makes stock “magically disappear” is the shrinkage of fabric that occurs after washing. A significant amount of loss can occur in this process depending on the type of fabric being used so this is something to track closely.
Once you have identified the process, you can now look into ways of estimating this anticipated loss more accurately: using our washing shrinkage scenario above, a first good step is to start measuring your fabrics after washing to find out their shrinkage rates and then apply these calculations to your recipe amounts so that your manufactures now allow for the extra quantity loss.
Another option would be to make regular manual adjustments for the shrinkage and note as such: in this way, you’ll be able to look back over your records and see exactly how much you “lost” via shrinkage. You can then use these adjustments to calculate your average shrinkage rates and then adjust your recipes going forward.
Again, try to spend some time in reassessing your pricing once you have found a hidden process: if you are using more materials than you thought your margins will have decreased so it may be time to bump up those prices a little to compensate.
Why accuracy is a Good Thing
There are many reasons for wanting to maintain accurate stock counts: doing it for the taxman for end of year reporting is only one of them.
It’s important to realise that the more accurate your manufacture records are in terms of material usage, the more accurate your pricing and profit estimating becomes as you now have much better awareness of your true costs.
You’ll want to aim for the situation where you have a minimal difference each time you do a manual count as this shows you that you are on top of your material usage and costs - this can take a while to get to this point depending on the complexity of your processes and it can be a frustrating journey at times.
Be patient and hang in there - it’s completely worth it in the end for the benefits it can bring to your business.
Inventory Cycle Count Best Practices
Now that you understand what a cycle count is and why it’s important for your business, let’s dive into some best practices to make the process as smooth and efficient as possible.
☑ Schedule Regular Counts
The key to maintaining accurate stock counts is consistency. By scheduling regular cycle counts, you can stay on top of your inventory levels and catch any discrepancies before they become too large to manage.
It’s a good idea to schedule counts during slower periods, such as at the beginning or end of each month. This will minimize disruptions to your production and shipping schedules.
☑ Prioritize High-Value Items
When conducting a cycle count, it’s important to prioritize high-value items first. These are typically your most expensive materials or finished products, so any discrepancies can have a significant impact on your bottom line. By prioritizing these items, you can quickly identify and correct any errors, ensuring that your inventory records are accurate for your most valuable assets.
☑ Use Technology to Your Advantage
Manual counting and recording of inventory levels is time-consuming and prone to human error. To streamline the process and improve accuracy, consider using technology such as barcode scanners or inventory management software. These tools can help you track inventory levels in real-time, automatically update records, and identify any discrepancies. This not only saves time but also reduces the potential for errors.
Read more: How to create UPC barcodes
☑ Involve Multiple Team Members
To ensure accuracy and accountability, involve multiple team members in the cycle counting process. This can include those responsible for production, shipping, and inventory management. By involving different team members, you can cross-check counts and catch any discrepancies that may have been missed by an individual. It also ensures that everyone is responsible for maintaining accurate inventory records.
☑ Continuously Review and Adjust Processes
As your business grows and changes, so too will your production processes and materials. It’s important to regularly review and adjust your cycle counting processes to reflect these changes. This can include updating count schedules, prioritizing different items, or implementing new technology. By continuously reviewing and adjusting your processes, you can ensure that your inventory counts remain accurate and efficient.
Inventory Cycle Count Software
Managing cycle counts doesn’t have to be a daunting task if the appropriate tools are used - cycle counting is a difficult process to map out using simple paper and pen situations, so it’s worth investigating more automated options as early as possible.
Cycle Count Spreadsheets
One of the simplest and most accessible ways to track and manage your cycle counts is through a spreadsheet.
Using applications like Microsoft Excel or Google Sheets, you can create a simple cycle count procedure template to allow you to count and record your stocktakes. You can log product details, track quantities, set a degree of automation for updating inventory levels, and even generate basic visual reports to help you spot trends or issues.
Another option is to use barcode scanners or RFID technology. These tools can significantly speed up the counting process, reduce human error, and update your inventory in real-time. They are particularly useful when dealing with larger inventories or when accuracy is paramount.
As an example, this thread from Reddit discusses how it is possible to connect a barcode scanner to Excel in order to undertake a simple cycle count.
However, while spreadsheets are a great starting point, they will not be able to scale with your business as it grows.
That’s where specialized inventory management software comes into play. Software like Craftybase is designed to not only manage cycle counts but also handle all aspects of your inventory management needs. It can automate many tasks, reduce errors, provide real-time updates, and generate detailed reports.
Remember, the best tool for your business will depend on your specific needs, budget, and the size of your inventory. It’s worth investing time to research and trial different options to find the perfect fit for your business.
Cycle Count using Craftybase MRP
Craftybase makes it easy to keep track of your business’s inventory with our automated cycle count software. Our intuitive, user-friendly system ensures you can always see what items are in stock and how much of them are on hand. This helps you make sure your inventory levels remain accurate without wasting valuable time counting each item individually.
You can create a cycle count using a variety of different criteria, whenever you like. This process allows you to quickly identify discrepancies between your inventory records and the actual numbers on your shelves. Once identified, our system will automatically suggest adjustments to make sure everything remains up-to-date and accurate.
Craftybase’s cycle count software also allows you to group items together with ease, so you can see which categories are most popular or need to be replenished.
Craftybase is here to make sure your inventory counts remain accurate and up-to-date, with no extra effort. With our automated cycle count software, you’ll have a clear picture of what’s in stock and what needs to be restocked.
Say goodbye to the hassle of manual counting and embrace the ease and efficiency of Craftybase (try our 14 day trial today!)to keep your inventory management running smoothly. Don’t let discrepancies and hidden processes affect your margins - make sure you have accurate stock counts with Craftybase.
Conclusion
Cycle counting is a more efficient and manageable way of keeping track of your inventory levels. By implementing this method, you can save time and reduce stress during stock counting periods, as well as catch any discrepancies before they affect your business operations. With careful planning and consistent execution, cycle counting can also help your business scale without sacrificing accuracy or productivity.
So don’t wait until the end of the year to count your entire inventory - start implementing cycle counting today for a smoother and more accurate stock control system.
Need to get your raw material and product inventory under control?
Try Craftybase - the inventory and manufacturing solution for DTC sellers. Track raw materials and product stock levels (in real time!), lot and batch tracking, COGS, shop floor assignment and much more.
It's your new production central.