Gross to Net Calculations for MRP: How They Impact on Small Manufacturing Businesses
In this article, we discuss how to calculate your Gross to Net Calculations for MRP and how they are important for small manufacturing businesses.
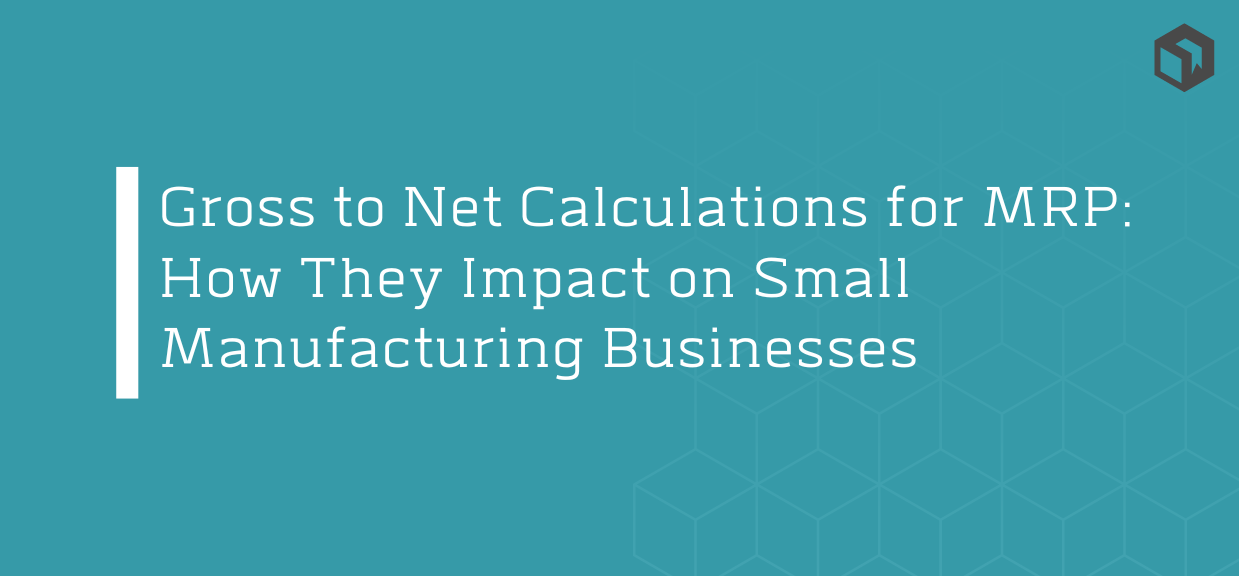
Gross to Net requirement calculations are essential for ensuring that a manufacturing company has the correct stock to hand, but this metric can be quite difficult to calculate.
In this blog post, we will discuss what gross-to-net calculations for MRP are, how to calculate your net, and why this metric is important for small manufacturing businesses.
Need to get your raw material and product inventory under control?
Try Craftybase - the inventory and manufacturing solution for DTC sellers. Track raw materials and product stock levels (in real time!), COGS, shop floor assignment and much more.
It's your new production central.
What is MRP?
Let’s start with a really brief overview of MRP. Manufacturing Resource Planning (MRP) is a system that helps manufacturing businesses plan and optimize their production processes. It takes into account all of the necessary costs associated with production, including materials, labor, and overhead expenses and allows a business to have full visibility of its entire supply chain.
What is a Gross to Net MRP Calculation?
An objective of MRP systems is to produce enough products to meet your required orders while keeping minimal inventory stock levels.
Your gross to net calculation is a metric that helps businesses understand their future material requirements, given their current raw material stock on hand and safety stock levels, and is a vital part of visualizing future stock production needs.
Without having accurate net requirement calculations, it’s impossible to determines gross material requirements: it’s difficult to know if you have too much or too little stock on hand to handle your future production needs.
If a small manufacturing business has too little raw material stock on hand, this can lead to delays in making products and getting them out the door - which can result in lost revenue, unhappy customers and bad reviews.
On the other hand, if a small manufacturing business has too much raw material stock on hand, it may be tied up in inventory that is not being used. This can lead to wasted resources and warehouse space, reduced cashflow and missed opportunities to sell finished products.
Therefore, it’s vital to ensure that your manufacturing business is always aware of its net requirements, and how to calculate it from your gross requirements.
The gross to net formula for MRP
This is how to calculate your gross to net requirement calculation for MRP:
Net Requirements = Gross Requirements - (Scheduled Receipts + On Hand Inventory)
So what does this mean? Let’s break this down into sections to make it easier to understand:
Gross Requirements
The amount of inventory you need, based on current orders and/or forecasted inventory needs
On Hand Inventory
This is the quantity of inventory that a business has on hand. This can be finished goods, raw materials, or work in progress.
Net Requirements
This is the gross requirements minus on hand (this is what you’ll need to fulfil your upcoming manufacturing orders). Your net requirement should ideally be above your specified safety (low) stock levels.
Calculating your Gross Requirements
To calculate your gross requirements, you essentially need to know:
- The number of products you need to manufacture (this may be a combination of placed orders and forecasted stock needs).
- How many raw materials are needed per product
- The lead time for each raw material (this is the amount of time it takes to receive the raw materials from your supplier)
To do this, you’ll want to create a master production schedule (MPS). The MPS is a high level plan that indicates when each end product will be produced.
It takes into account the lead times of all the raw materials and components needed to produce the finished good, as well as your available manufacturing capacity given current staffing levels.
The MPS is then used to generate a production plan that schedules when each raw material and component will be needed.
In order to calculate the gross requirements, you’ll also need to create a bill of materials (BOM) for each product in your line.
The BOM is a list of all the raw materials, components, and sub-assemblies that are required to produce a finished product. It can be calculated either on an individual or a batch level (i.e the raw materials list can be defined in terms of how much you need to create a batch or per product).
Once you have product level BOMs and a production schedule you can then begin to calculate your gross requirements for the period you need to review.
Check out our free BOM template for Excel and Numbers here →
On Hand Inventory
Once your gross requirements have been calculated, you can then begin to look at your on-hand inventory levels and scheduled receipts to determine your net requirements.
On Hand Inventory
This is the quantity of inventory that a business has on hand. This can be finished goods, raw materials, or work in progress.
Scheduled Receipts
These are the raw materials, components, or sub-assemblies that a business has on order from suppliers. These are important as the lead time for each item will need to be taken into account to calculate when the materials will arrive and be available for your production process.
By subtracting the scheduled receipts and on-hand inventory from the gross requirements, businesses can then determine their net requirements.
Safety Stock Levels
As part of figuring out your gross to net calculations, you’ll also want to spend some time calculating your safety stock levels.
Your safety stock levels are the minimum amount of inventory you should have on hand, in order to avoid any disruptions in your production line. It’s therefore a really important metric for any small manufacturing business.
There are a number of different factors that go into calculating safety stock levels, including:
-
The variability of demand
-
The lead time for receiving raw materials
-
Your desired service level to your customers
It’s important to note that safety stock levels are not a one-time calculation. They should be reviewed and updated on a regular basis, as your business changes and grows.
Calculating Your Net Requirements
Now that you know how to calculate your gross requirements and safety stock levels, you can finally begin to calculate your net requirements using the formula.
As we mentioned before, your net requirements are equal to your gross requirements minus on hand inventory.
Systems to automate your gross to net MRP calculations
Although it is technically possible to wrangle a spreadsheet into calculating your gross and net calculations for you, these calculations can get very hard to manage if you have many products and complex sub-assemblies so it isn’t a recommended approach for small manufacturers looking to scale.
MRP and ERP software are systems that can help automate gross to net calculations for MRP.
ERP (Enterprise Resource Planning) systems are solutions that integrates all of the different departments within a company. This includes a range of different operations including manufacturing, accounting, sales, and customer service.
MRP (Materials Resource Planning) software is a subset of ERP and is specifically designed for manufacturing businesses by helping them plan and optimize their production processes. It takes into account all of the necessary costs associated with production, including materials, labor, and overhead expenses so can be used to generate your gross and net calculations for you.
If you’re a small manufacturing business, we recommend investing in an ERP or MRP system early on to help track your on hand inventory, future requirements and thus streamline your gross to net calculations for MRP.
Introducing Craftybase: the MRP for small manufacturing businesses
Craftybase is an MRP software system designed specifically for small businesses in the manufacturing industry. We help automate your gross to net calculations for MRP, as well as a range of other time-consuming tasks such as tracking inventory and calculating landed costs (including shipping and tariffs).
We offer a free 14 day trial so you can try out our features for yourself, and we have a team of experts on hand to answer any questions you might have.
Why not sign up today and see how Craftybase can help your small manufacturing business?