How to calculate Cost of Goods Sold using the Weighted Average Method
We show you how to calculate your COGS using weighted (or rolling) averaging costs.
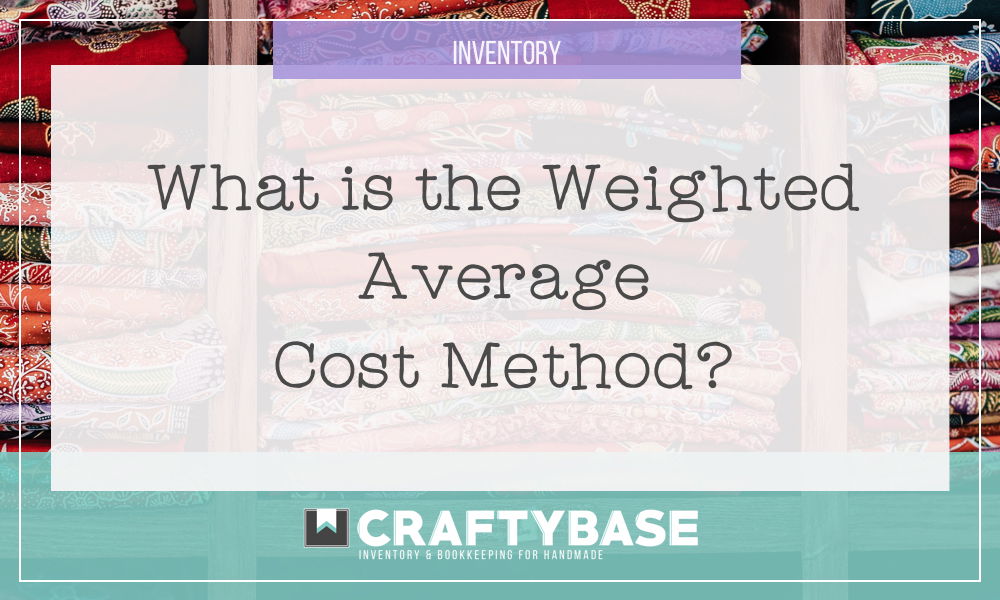
In the dynamic business world, understanding your company’s financial health is crucial. One critical metric is the Cost of Goods Sold (COGS), which influences gross profit and net income. This article explores the Weighted Average Method, a popular approach to calculating COGS.
It ensures a more accurate representation by considering fluctuations in inventory cost. Don’t let the jargon intimidate you - we’ll break down the steps in a simple, straightforward manner to help you master this essential financial tool.
Need to get your raw material and product inventory under control?
Try Craftybase - the inventory and manufacturing solution for DTC sellers. Track raw materials and product stock levels (in real time!), COGS, shop floor assignment and much more.
It's your new production central.
What is Weighted Averaging?
Weighted Averaging (or “rolling averaging”) is a method of calculating an average by assigning each item in the set or data points a weight based on its relative importance. In other words, it considers both the value and quantity of each item to determine the overall average. This approach is commonly used in various fields, including finance, statistics, and economics.
In perpetual inventory systems, weighted averages are used to provide a high level of accuracy to your material and product costings - especially when there are significant fluctuations in inventory prices over time.
How can I calculate a weighted average?
Although most people learned how to calculate a simple average from their high school days, weighted averages are not something that many people have seen or needed to calculate directly. You have however most likely been impacted by weighted averages without perhaps knowing it.
☞ Need to get your [raw material](/blog/what-does-raw-materials-mean/) and product inventory in control? Try Craftybase - the inventory and in-house manufacturing solution for DTC sellers. Track [raw materials](/blog/what-does-raw-materials-mean/) and product stock levels (in real time!), COGS, shop floor assignment and much more. It's your small business' production central. Start your free 14-day trial today →
One common example of weighted averages is school grades: when calculating your final grade for the year, most teachers will apply different weightings to each of your assignments and tests - they don’t just simply add up each score and divide it by the number of tests you were given. Instead a weighting of relative effort is usually applied to each testable item - this ensures that final exams or major assignments are factored into your final grade in a much bigger way than weekly quizzes and other minor homework tasks.
The definition of a weighted average is therefore an average that has been assigned a relative importance (“weight”).
Why is a weighted average important for inventory?
Essentially, the average will only find the “middle” value regardless of any other factors - this can be problematic for inventory calculations as you will have situations where your stock value will change throughout the year based on how much you buy and what unit price you purchase it for. Weighted averages factors in these cost differences each time you purchase the material.
Going back to our school grades example, the weighting used was “relative effort”. In inventory accounting, weighting is given based on the quantity of stock available at a certain point in time.
Let’s work through a simple example. Let’s say you have two units of a material: one unit was purchased at $10 and another unit was purchased later on at $20.
As a quick reminder, the formula to use to calculate an average from a set of numbers is:
The average cost of the material in our example above is therefore:
($10 + $20) ÷ 2 = $15
Let’s now calculate an example where there are different quantities of each unit cost involved. If one unit of your material was purchased at $10, but two units were purchased at $20 then we should expect the average should go slightly up:
($10 + $20 + $20) ÷ 3 = $16.60
The average is now slightly higher. This is due to the extra weighting placed on the two $20 items as there were more of them to consider.
For perpetual inventory weighted averages, this calculation is constantly (or “perpetually”) calculated whenever a stock change is made to your material’s inventory. This is known as a rolling or moving average (as it changes as you move forward in time).
This ensures that the calculation factors in the current quantity available and the cost of each every time. This is quite understandably a tedious calculation to make, which is why you will most likely be using an inventory system that does this automatically for (like Craftybase) rather than doing this yourself by hand.
Let’s now look at the example above represented as stock changes (purchases only) in an inventory system:
Date Purchased | Unit Cost | Quantity | New Stock on Hand | New Average Unit Cost |
---|---|---|---|---|
1 Jan | $10 | 1 | $10 | $10 |
3 Jan | $20 | 2 | $10 + $20 + $20 | $16.60 |
If I was to take my stock value on the 1st Jan, I would have a value of $10. On the 3rd Jan, I add a new purchase to my inventory system which then triggers a recalculation of the average to $16.60.
To add to this, remember that each and every stock change in the perpetual inventory system will recalculate your average. Let’s record the dates of usage of materials as well as purchases and see what happens to the averaging:
Date | Unit Cost | Quantity Change | New Stock on Hand | New Average Unit Cost |
---|---|---|---|---|
1 Jan | $10 | +1 | $10 | $10.00 |
3 Jan | $20 | +2 | $10 + $20 + $20 | $16.60 |
4 Jan | $20 | -1 | $10 + $20 | $15.00 |
In an inventory system, rolling averages are used not only for material unit costings but also for the overall cost of manufacturing (or purchasing) the goods you sell: this allows the system to be able to calculate your inventory value and COGS.
In the product example, making the item increases your stock and selling the item decreases your stock: the cost to make the stock is therefore calculated when either of these things occur.
More details on how COGS (Cost of Goods Sold) can be found here How do I calculate Cost of Goods Sold (COGS)?
For more information on how Weighted Average Cost differs to other Inventory Cost methods such as LIFO and FIFO, please see our blog post here: Which method of valuing inventory is best for your handmade business?
Why should businesses adopt weighted average costing for inventory?
-
More accurate cost reporting: Weighted average cost method involves taking into account the cost of all inventory items on hand and the number of units available, which provides a more accurate cost per unit.
-
Simplicity and efficiency: The method is easier and more straightforward to implement than other methods such as LIFO or FIFO as it doesn’t require tracking of individual inventory item’s purchase dates or costs.
-
Buffer against price volatility: By spreading the cost over the total number of units, the weighted average cost method can help cushion the impact of sudden price changes in the cost of goods.
-
Consistent pricing: It allows for consistent pricing of products, enhancing the reliability of financial records and inventory valuation.
-
Reduced risk of obsolete inventory valuation: Unlike FIFO or LIFO, the weighted average method helps to prevent obsolete inventory values as it continually includes all costs in the calculation.
Software options for weighted average costing
Performing complex calculations like weighted averages manually can be an arduous and time-consuming task. It requires careful attention to detail and meticulous tracking of numerous variables that can easily lead to errors, especially when dealing with large inventories.
Similarly, while Excel spreadsheets might seem like a handy tool for maintaining and calculating inventory costs, they too can quickly become cumbersome. Crucially, they don’t scale well with increasing inventory size and complexity.
There are several software options available that can help businesses easily implement weighted average cost methods for inventory valuation, including Craftybase (which we will discuss in detail blow), Quickbooks and FreshBooks. These systems provide automated calculations of the weighted average cost and other financial reports related to inventory management. This saves businesses time and minimizes human error in manual calculations.
Moreover, these software options also offer additional features such as tracking inventory levels, managing orders and generating financial reports, making them valuable tools for businesses looking to streamline their operations.
Craftybase - your solution for weighted average calculations
Craftybase is a popular COGS software option for small manufacturing businesses, offering an all-in-one solution to manage inventory and product costing.
With its intuitive user interface and robust features, Craftybase makes it easy for businesses to adopt weighted average cost methods for inventory valuation.
In addition to calculating weighted averages, Craftybase also offers features such as batch tracking, order management, and inventory level tracking. It also integrates with popular e-commerce platforms such as Etsy, Shopify and WooCommerce, making it an ideal choice for businesses selling handmade goods online.
Try Craftybase for 14 days, completely free, today!
Conclusion
In conclusion, the weighted average cost method is a reliable and efficient way for businesses to value their inventory.
By adopting this costing method, businesses can enjoy more accurate cost reporting, simplified processes, buffer against price volatility and consistent pricing of products. With the help of software options such as Craftybase, implementing this method becomes even simpler and more effective.
So if you’re a business looking to streamline your inventory management and valuation processes, consider using the weighted average cost method today. So why not start using it for your business today? You’ll be able to enjoy all the benefits mentioned above and have peace of mind knowing that your inventory is accurately valued.