What's the difference between perpetual and periodic inventory? A guide for small business
We explain, in simple terms, periodic and perpetual inventory systems and the pros and cons of each.
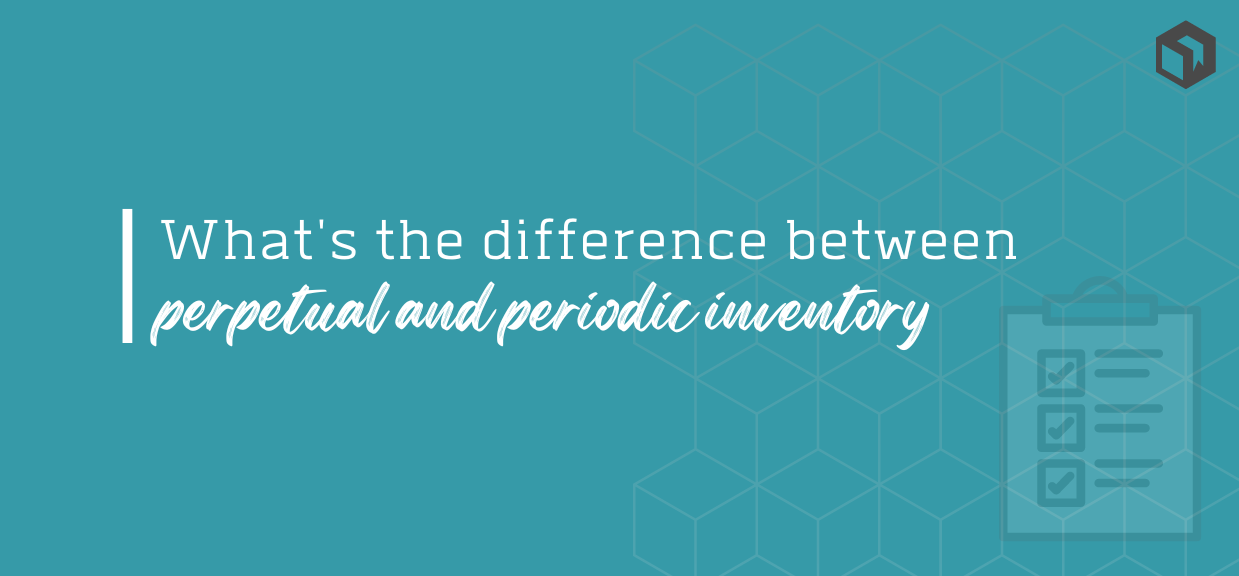
The IRS and GAAP (Generally Accepted Accounting Principles) rules both state that you have the choice to either count your complete inventory on an annual basis once a year or maintain a perpetual (constantly counting) counting system. So, which method of tracking is generally best?
Need to get your raw material and product inventory under control?
Try Craftybase - the inventory and manufacturing solution for DTC sellers. Track raw materials and product stock levels (in real time!), COGS, shop floor assignment and much more.
It's your new production central.
To find out, we’ll cover everything you need to know about periodic and perpetual inventory management systems, including some examples so you can see how they work in practice.
What’s inside:
Let’s start with some definitions:
Periodic inventory systems
Periodic Inventory involves counting and recording your stock levels every once in a while (i.e. on a “periodic” basis). For most small businesses that use this approach, this count only occurs annually to provide financial figures for tax purposes however you can also use this method quarterly or even monthly if your workflow allows. Most periodic systems tend to be very simple inventory spreadsheets or paper journals.
The periodic method involves stopping all production and sales on a specific date and then undertaking a complete count of your inventory in this “frozen moment in time”.
The number on hand is noted, along with a calculated unit price in your periodic inventory system. Your quantity on hand multiplied by your unit price becomes your material inventory valuation for the material.
This method is relatively easy if you have a very small inventory as you only need to set aside a day or so at the end of the year to do your basic count, however can be tricky to calculate materials that are now tied up in your unsold stock and the true “landed cost” of your materials.
Because you are only counting your stock at the end of the year, you won’t have much visibility on your actual stock levels, so you’ll need to be “eyeballing” your stock regularly to determine what materials you are running low on. You’ll also be completely unaware of any unexpected stock loss (i.e. damaged stock) so can do little about this situation when it is found at the end of the year.
Periodic inventory accounting
In terms of your accounting, only information gathered during your physical counts can be used to balance your ledgers. Usually this involves adding the balance to your beginning inventory at the start of the next financial period.
Ending inventory and COGS are also done at the end of the financial period in an periodic system for the same reasons - in between these financial start and end periods, only estimates of material usage, inventory and COGS can be generated and used for reporting and forecasting.
Industries and businesses that suit periodic inventory
Periodic inventory tracking systems usually only suit very small business operations, this is mostly due to the physical and manual requirements involved.
If your business has more than one warehouse or physical location for your stock, periodic inventory is not recommended unless you have a way of tracking stock transfers between locations.
It can however be an excellent starting point to inventory management for very small businesses that are not looking for significant growth, or are not looking to expand their operations outside one physical location. Periodic inventory can also be a good solution if a business isn’t clear about their exact requirements in terms of featureset - once this is defined, then a perpetual system can be found that meets these needs.
Pros of periodic inventory systems
- The periodic system is relatively easy if you have a very small inventory as you only need to set aside an hour or two at the end of the year to do your basic count (but don’t forget to also count any materials tied up in your unsold stock!).
- If the purchase prices of your materials haven’t varied, or if you haven’t restocked very often through the year unit prices can often be fairly simple to calculate by hand.
- As a consequence of this method’s simplicity, it is quite appropriate to use simple systems like paper books or spreadsheets to track and count.
Cons of periodic inventory systems
- As you are not keeping records of inventory levels during the year, you’ll need to constantly be “eye-balling” your stock levels to ensure that you don’t run out of materials you need to produce your products. This in reality means several ad-hoc stocktakes through the year rather than the one, so you’ll need to factor this time in.
- If you have a large inventory, once a year counts can be very time intensive and prone to error - especially if you are a solo entrepreneur trying to get orders out at the same time.
- If you purchase many lots of the same materials at different prices during the year, calculating your unit price can be time consuming and difficult.
- This system puts all the work at the end of the financial year when your figures are due: this is one of the most stressful times in the year for a small business. For self-employed people, having an unexpected event occur around this time (sickness, large influx of orders) could jeopardise your chances of getting these numbers together in time for the deadline and thus you risk the chance of fines.
- Your COGS (Cost of Goods Sold) final figure will not be known until year end, so you’ll need to be ready for an unexpected tax total if your cost of manufacture is less than expected.
- This system doesn’t tend to scale well as you grow your business - eventually you’ll need to switch to something more robust when your inventory and purchasing activities become too complex to track using spreadsheets and paper.
- It can be difficult to keep your records with enough granularity to satisfy IRS auditing - you’ll need to make sure that you “show your working” for any material unit cost calculations you are doing manually and ensure that they are in line with the IRS recommendations (i.e. FIFO, LIFO or Rolling Weighted Average)
Perpetual inventory systems
The word ‘perpetual’ means doing something on a continuous, ongoing basis.
Perpetual inventory means that the counts and calculations are done constantly in real-time rather than at certain times during the year.
Rather than updating a spreadsheet with new counts each year, you update a system with stock changes as they occur: when you make your product, sell it, or purchase new stock. This gives you real-time stock and valuation data so that you can see your exact stock situation at any time.
By using perpetual inventory systems, a business can also adopt a number of automated processes like barcode or QR scanning or even RFID tagging to track goods as they move in and out of the warehouse locations.
Some examples of popular perpetual Inventory systems include Craftybase, Quickbooks Manufacturing, and Unleashed.
A perpetual system does all the calculations that are required to produce the numbers you need. You’ll, however be responsible for entering in the data for your expenses and manufactures as they occur and manually checking for accuracy via regular stocktakes.
A big advantage to using a perpetual inventory management system is seeing stock levels in real-time, as this provides the ability to react to low stock situations quickly…and even predict when they will occur ahead of time.
Stocktaking using the cycle count approach allows you to further assess and refine your usage of materials and make improvements to your processes throughout the year.
Pros: perpetual systems offer businesses greater accuracy when it comes to tracking their inventory levels, meaning they can better predict demand and make more informed decisions about their production lines.
Cons: perpetual systems are more expensive to implement and require a lot of resources to maintain.
Pros of perpetual inventory systems
- More accurate than periodic systems
- Always up-to-date, with real time data available at all times
- Lower risk of stockouts or overstocking due to stock visibility
- Allows for Work in progress (WIP) accounting
- Suitable for inventories of all sizes
- Provides real-time cost of goods sold (COGS)
- Access to more data to guide business decisions
- Less internal time wasted on stocktakes and manual accounting
- Reduced risk of human errors during stocktake
Cons of perpetual inventory systems
- Steeper learning curve to learn accounting principles
- Takes time to properly implement processses around managing stock
- Events must be logged in real-time and correctly to get accurate counts and valuations
- Extra costs for dedicated software
- Occassional stocktakes are still recommended for accuracy checking
Examples of perpetual and periodic inventory systems
Now that you understand the difference between periodic and perpetual inventory systems, let’s look at an example of how each works for small businesses.
Periodic inventory example: Jim
Jim owns a woodworking business and has a team of 3 staff. Jim is currently using a periodic inventory system, which means he and his staff take a physical inventory count on the 1st of every month.
This involves walking around the workshop, counting each raw material and finished product, and entering the updated count in their Excel inventory spreadsheet.
During the month, Jim doesn’t know his exact stock levels and can only make manufacturing and purchase decisions after the monthly count is complete.
To create a view of total inventory value on hand, Jim can estimate this by multiplying his average unit cost per material or product by the amount in stock. This is an estimate as it does not account for the amount of stock bought at different prices throughout the year.
Perpetual inventory example: Kate
Kate owns an apparel manufacturing company with a team of 5 staff members. Kate uses a perpetual inventory system, which means she and her staff are continuously tracking inventory levels as goods move in and out of their warehouse.
Each time a raw material is purchased, the team updates its online inventory platform with the quantity purchased. The system automatically calculates the new inventory stock level for that material.
When a finished product is shipped, the system is then also updated to reflect the deduction in inventory to show real-time product stock levels.
This means Kate and her staff have visibility of their inventory stock levels at any given time, allowing them to make informed decisions about their product line and purchase orders.
Kate can also calculate a very accurate inventory valuation based on her stock on hand, as her perpetual inventory system tracks each purchase of raw materials / product and it’s usage / sale.
Conclusion
The IRS and GAAP (Generally Accepted Accounting Principles) rules both states that you can either count your complete inventory on an annual basis once a year or maintain a perpetual (constantly counting) counting system. This means that both perpetual and periodic inventory systems are both fully tax-compliant solutions in the US.
The decision to adopt either a periodic or a perpetual approach to your inventory thus falls to the systems and processes you currently have and are willing to implement.
Perpetual systems require a business to have good processes for the checking in of new stock, and the release of sold stock. For manufacturing businesses, tracking when products are made using which raw materials is also extremely important.
No matter which inventory system you choose, it’s important to ensure that it is updated as often as practicable so that you can make the right purchasing and forecasting decisions for your business.
Introducing Craftybase - Perpetual Inventory Software for Small Manufacturers
At Craftybase, we understand the importance of having accurate inventory data in order to run your small manufacturing business effectively. Our perpetual inventory system allows you to track raw materials and finished products with ease, giving you full visibility over your stock levels at all times.
With our software, you can easily update your inventory records as materials are received and products sold, giving you the data you need to make informed decisions about your product line.
We save small businesses time, money and resources by streamlining their inventory management processes so they can focus on building their products with confidence. Try Craftybase for free today and see how our software can help revolutionize your inventory system.