What is inventory shrinkage?
We discuss inventory shrinkage and how you can better manage inventory loss as part of your manufacturing process.
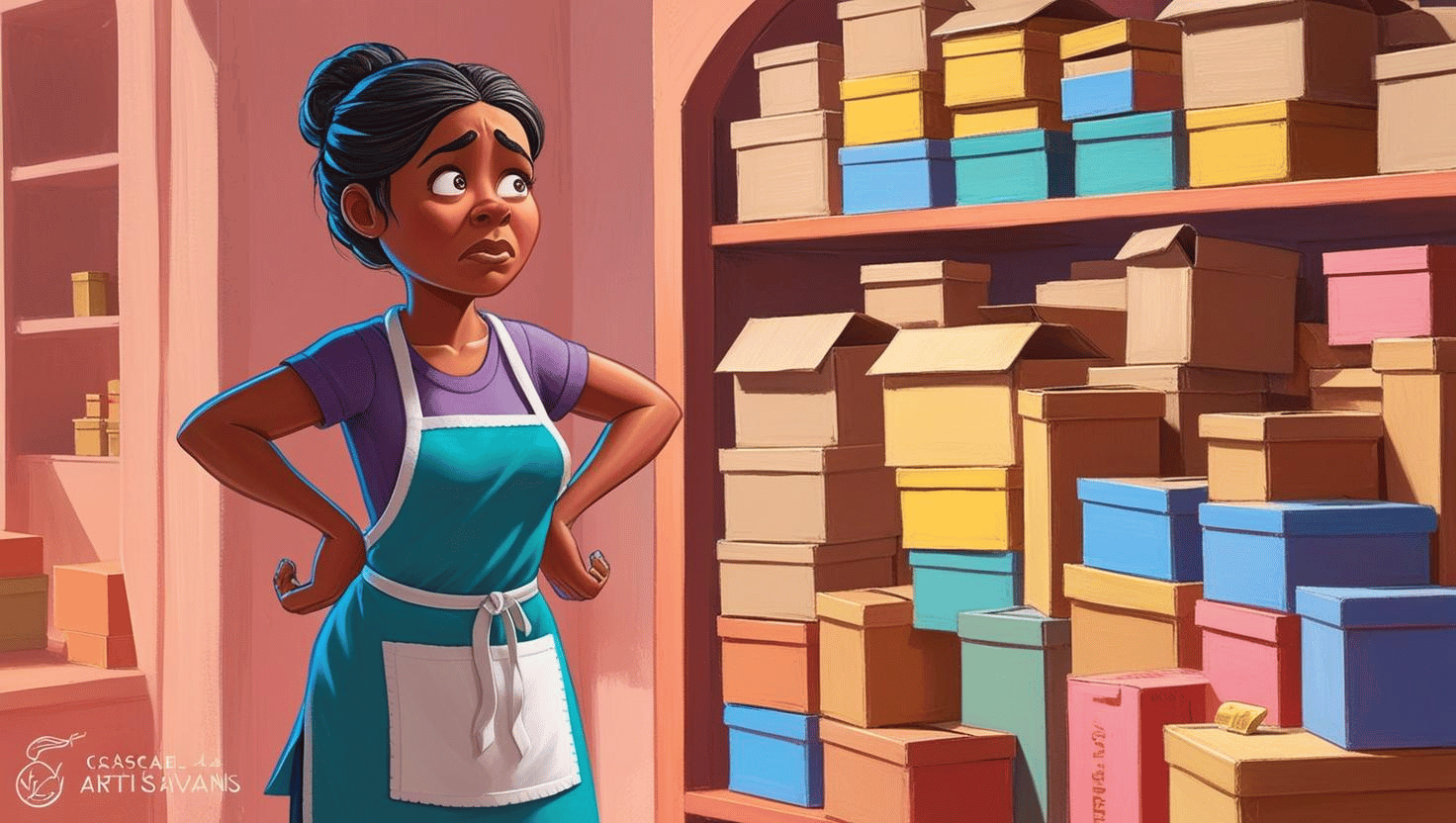
Inventory shrinkage—when your actual stock doesn’t match up with your records—can be a real headache for Etsy sellers. It’s like thinking you have three of those best-selling necklaces ready to ship, only to find out you’re short when orders roll in.
Inventory shrinkage is a significant concern for most businesses, leading to substantial financial losses annually. According to the National Retail Federation, retail shrinkage resulted in $112.1 billion in losses in 2022, marking a nearly $20 billion increase from the previous year. In other words: you aren’t alone.
In this blog post, we will discuss ways that you can firstly identify, then reduce your inventory shrinkage and thus improve your inventory management and manufacturing processes.
Need to get your raw material and product inventory under control?
Try Craftybase - the inventory and manufacturing solution for DTC sellers. Track raw materials and product stock levels (in real time!), COGS, shop floor assignment and much more.
It's your new production central.
What is inventory shrinkage?
Simply put, inventory shrinkage is the difference between the inventory you think you have (based on your records) and what’s actually on your shelves.
There can be many reasons why the material has been removed from your inventory, with each cause requiring a slightly different approach to analyse and improve on. It’s worthwhile to be aware of how much material shrinkage you currently have so you can address the causes where possible and ensure that you are factoring it into your costs of production.
Common Causes of Inventory Shrinkage
Employee Theft: Internal theft is a leading cause of inventory shrinkage. Employees with access to stock may misappropriate merchandise, especially in environments lacking robust security measures.
Shoplifting: External theft by customers, particularly in retail settings, contributes significantly to inventory loss. Small, high-value items are especially vulnerable.
Administrative Errors: Mistakes such as incorrect data entry, pricing inaccuracies, or miscounts during stock audits can create discrepancies, leading to shrinkage.
Vendor Fraud: Suppliers may engage in fraudulent activities like inflating invoices or delivering fewer items than billed, resulting in inventory discrepancies.
Damage and Spoilage: Products damaged during handling, storage, or transportation, as well as perishable goods that spoil before sale, contribute to inventory shrinkage.
Why is it important to track and analyze your inventory shrinkage?
There are a few key reasons why it’s important to track and analyze your inventory shrinkage:
To identify areas of waste in your manufacturing process
By understanding where and why your raw materials are being removed from your inventory, you can make changes to your process to reduce or eliminate the waste. This can save you money in the long run by reducing the amount of raw materials you need to purchase.
To understand the impact on your bottom line
Inventory shrinkage can have a significant impact on your business’s bottom line. By tracking and analyzing your inventory shrinkage, you can get a better understanding of how much it is costing you and make changes accordingly.
To improve your forecasting
If you know how much inventory shrinkage you typically experience, you can account for it in your forecasting. This will help you avoid overstocking (which can tie up capital and lead to storage costs) or understocking (which can lead to lost sales).
What are some ways to prevent inventory shrinkage?
There are a few key ways that you can reduce inventory shrinkage:
Track your inventory
By tracking your actual inventory on a regular basis, you can catch issues early and prevent them from becoming bigger problems. This can be done manually or through the use of technology, such as barcoding and RFID tagging.
Reduce waste
One of the main causes of inventory shrinkage is waste. By reducing waste in your manufacturing process, you can reduce the amount of raw materials that are removed from your inventory.
Improve security measures
Another common cause of inventory shrinkage is theft. By improving security measures, such as CCTV and access control, you can deter thieves and protect your actual inventory.
How to calculate inventory shrinkage
There are a few different ways to calculate inventory shrinkage. The most common method is to use the “retail inventory method.” This method estimates shrinkage by comparing the value of your ending inventory to your sales and cost of goods sold (COGS).
To calculate inventory shrinkage using the retail inventory method, you will need to know the following:
Your ending inventory value
This is the value of your inventory at the end of the period you are measuring. This is confirmed via a physical inventory count, usually performed at the end of the financial year.
Your sales
This is the total value of your sales during the period you are measuring.
Your COGS
This is the total cost of the goods sold during the period you are measuring.
Once you have this information, you can calculate your inventory shrinkage using the following formula:
Inventory Shrinkage = (Ending Inventory Value - Sales - COGS) / Sales
For example, let’s say that your ending inventory value is $100,000, your sales are $200,000, and your COGS is $150,000. Using the formula above, we can calculate that your inventory shrinkage percentage is 25%.
How to handle inventory wastage in your bookkeeping process
If you want to avoid overstocking, it’s important to track and manage inventory wastage. Wastage can occur for a number of reasons, such as damage, expiration, or spoilage. When it comes to bookkeeping, there are a few different ways to handle inventory wastage:
Materials removed from inventory that have been damaged
This usually occurs when the material has been somehow damaged whilst stored.
This is normally accounted for via a simple stock “write down” adjustment to your inventory stock on hand. However, if the material has been damaged in the direct production process, it may be better to include this cost into the manufacture materials cost where it will be accounted for as material usage.
Miscounts of materials from prior stocktakes
This can happen when in a previous inventory stocktake the number in available stock was incorrectly recorded, so you now have less of a material than your records currently indicate.
Ideally, the way to rectify this is to review your material purchase records to try and reconcile the difference, then adjust your expense history to ensure the tally is now correct. If you cannot locate the source of the discrepancy, then you should make a stock level adjustment in your inventory bookkeeping program to get your records back in sync with your physical stock.
Underestimating your previous material usage
If you use an inventory materials tracking system and you have under-estimated of the amount of materials required to create your piece, this will result in an inventory deficit when you next do a stocktake. This commonly occurs when the true amount of “scrap” produced is not adequately accounted for: as most scrap cannot be returned to your materials inventory and needs to be discarded, this can lead to a shortfall in your inventory.
In this case, it is better to include a more accurate measurement of the average percentage of “Scrap” that is normally created in the production of your product in your Bill of Materials, than to periodically mark it down via a stock shrinkage adjustment.
Spoilage of materials
Some of your materials may have a shelf life whereby if they haven’t been used by this time then the material is said to be spoiled and can no longer be used. Your inventory amounts, therefore, need periodic adjustment to ensure that only the usable materials are counted in your stock on hand. It is a good idea to create inventory adjustments rather than reduce the quantity on hand number so you can track the percentage of overall wastage from spoilage: if this percentage is quite high, it could indicate that you need to ensure you only keep a minimum of spoilable materials on hand at any one time.
It is often a good idea to invest in an inventory management program to help track your materials.
Craftybase - your solution to managing inventory shrinkage
Craftybase is the perfect solution for managing your inventory and avoiding shrinkage. With our powerful software, you can track your materials, estimate Scrap percentage, and set reorder points to avoid running out of stock. We make it easy to keep your books in order and improve your manufacturing process. Try Craftybase today!