What does GMP stand for in Manufacturing?
We discuss what GMP stands for in a manufacturing sense and how it is important to your small maker business.
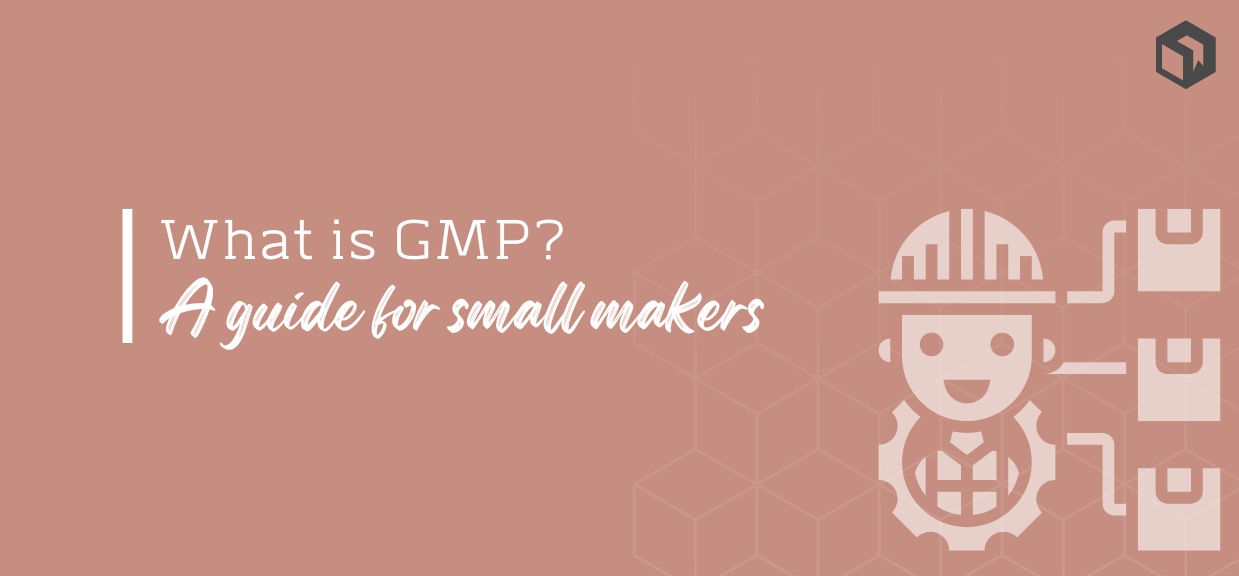
No matter the size of your business, if you make food, cosmetics, or any other products designed to be consumed by people you will need to be in compliance with the GMP requirements of your country and any other countries you sell your products in.
Need to get your raw material and product inventory under control?
Try Craftybase - the inventory and manufacturing solution for DTC sellers. Track raw materials and product stock levels (in real time!), COGS, shop floor assignment and much more.
It's your new production central.
What is GMP?
The term “GMP” stands for “Good Manufacturing Practices”. GMP is a set of guidelines that dictate how manufacturing should be carried out in order to produce consistent, high-quality products.
GMP covers all aspects of manufacturing, from raw materials to finished products. It includes procedures and processes that must be followed to ensure that products are made safely and accurately.
GMP is not a law, but it is closely linked to the legal requirements of many countries. To sell your products in certain markets, you will need to demonstrate that you comply with those countries’ GMP requirements.
There are different grades of GMP, depending on the product type. For example, food-grade GMP is different from cosmetic-grade GMP.
GMP guidelines are constantly evolving, and it is important to keep up to date with the latest requirements. Failure to do so could result in your products being rejected or recalled.
Why is GMP important?
GMP is important because it helps ensure product safety and quality. By following GMP guidelines, you can be sure that your products are made to a high standard and are safe for consumption.
This is especially important for food and cosmetic products, as people are directly exposed to them. GMP ensures that these products meet the required safety standards.
GMP is also important for protecting your business. If you are found to be non-compliant with GMP requirements, you could face serious consequences, such as hefty fines or even a prison sentence.
Following GMP guidelines can also help improve your manufacturing process’s efficiency. By streamlining your procedures and processes, you can save time and money.
How do I comply with GMP?
The first step is to familiarize yourself with the GMP requirements of your country. You will need to ensure that you are complying with all of the relevant regulations. For the purposes of this article, we’ll be taking a deep dive into the GMP regulations that are applicable to US based small manufacturing businesses.
It is your responsibility to create your own custom processes based on the guidance to develop a workflow that ensures your products conform to GMP.
A big important point here is that all businesses, no matter how small, need to ensure that they conform to the regulations.
Although at times, the language in the GMP documentation seems to indicate this is for big factory operations with legions of staff, it’s also important to note that it is all completely applicable and enforceable for small maker businesses like yours.
The basic guidelines (or tenets) of GMP are:
-
The product should be free from contamination
-
The product should be consistent in manufacture
-
All manufactures should be well documented
-
All staff making products should be well trained
-
The product should be checked for quality throughout the manufacturing process
The US CGMP (Current Good Manufacturing Practice) is monitored and enforced by the FDA, whereas in Europe it is known as Regulation EC 1223/2009. Similar systems exist in Canada, Australia and China amongst other countries.
Let’s take a closer look at the FDA’s Cosmetic Good Manufacturing (GMP) Guidelines for Cosmetics as an example to see how the GMP processes generally work. The FDA CGMP applies to anyone manufacturing soap or beauty products in the US.
Documentation
Documentation should capture every aspect of your manufacturing process - you will need to, at a minimum, write down your recipes with as close to exact measurements as possible, and log when you create new batches of your products.
The goal of your documentation is that you’ll be able to trace back any problems with your production process and pinpoint the likely cause.
Records
This is the actual method you choose to document your production process. Your records can be in either paper or electronic format, however, you’ll want to ensure that you have backup procedures in place for both - for paper this means keeping another copy of all records off-site in case of fire or water damage; for computer based records you’ll want to ensure that you have another backup created on a different machine or “in the cloud”.
You’ll need to be recording the origin and receipt of your raw materials: this is essentially where you purchased it from and any identifying lot numbers that can be used to trace back issues to a fault of this raw ingredient.
Tip: Craftybase MRP is designed to handle tracking of raw materials from purchase right through to eventual sale and provides you with the traceability you need for your records.
Batch Production Control Records
For each batch manufacture, you’ll want to record the name, code, lot number and quantity used in the batch, along with how the batch was manufactured.
In-process sampling and adjusting steps should also be a part of your manufacture record - this is for situations where you may tweak the recipe by adding a small amount of a material (i.e a couple of drops more of a fragrance that may be less aromatic than usual).
Each of your manufactures should be assigned a unique product lot number and should be clearly documented as to if this resulted in a sellable product.
Read more: Why you should care about lot numbers »
Testing procedures and results also need to be factored into your records. This should include your testing procedures (how you test for quality and when), when the tests were carried out and the results.
Your goal for this area is to collate records that allow you to identify and conduct an effective recall of stock.
Buildings and Facilities
You’ll want to ensure that any area in which you manufacture your products are sized and designed appropriately for their use and also clean and orderly.
The size and design requirement is mainly to ensure that you have the space to prevent cross contamination or mix-ups between materials (i.e. accidental spillage or splashes between different batches being made at the same time).
The area needs to be clean to ensure that no outside environment contamination occurs (dust, animal hair etc.). This isn’t just limited to workspaces: you’ll need to ensure that walls and ceilings need to also be clean and created from easily cleanable surfaces. Attention to dust, humidity and temperature is also important to ensure that contamination does not occur.
Washing and cleaning processes for the area, along with facilities, machines, equipment and tools also needs to be considered.
Equipment
All equipment and utensils involved in the manufacturing process need to be appropriate to their usage. This essentially means that you shouldn’t be using a rusty old spoon handed down from your grandma to stir your batches when a latex spatula would be a better choice from a contamination and sanitary perspective.
All utensils and work surfaces should be:
-
clean
-
orderly
-
sanitized as often as possible
-
covered or stored away from dust and other contaminants
For any measuring equipment, this needs to be calibrated and checked on a regular basis to ensure that your ingredients are being measured out accurately.
Any defective or broken equipment should be immediately fixed or removed from use.
Personnel / Staff
This section involves processes for yourself and anyone that works with you. It essentially involves ensuring all staff have adequate training and experience to carry out their assigned functions.
Read more: Training and managing staff for your maker business »
All staff that come into contact with the production process or raw ingredients need to be wearing clean clothing and any protective gear that are necessary to providing a contaminant free work area (i.e hair restraints and snoods for men’s beards).
Personal levels of cleanliness also need to be maintained. This means stringent hand washing routines and covering of any open wounds or injuries that could potentially come in contact with products or materials.
Eating, drinking or smoking should be restricted to areas outside of your work and storage areas.
Your workspaces should also be available only to trained staff - customers and family members should not be allowed to access these areas without supervision.
Raw materials
Raw materials need to be able to be identified at any stage in the production process.
All materials need to be stored in accurately labelled containers to prevent mix-ups or selection mistakes. These labels should not only display the name of the ingredient clearly, but also any unique codes, lot numbers and control statuses (i.e. “quarantine” if not currently available for use due to a failed test).
Read more: How to properly label your materials »
Materials should be stored separately in closed storage containers in a position off the floor to prevent cross-contamination.
Materials should also be stored in a manner that reduces exposure to environmental conditions (i.e. away from direct sunlight, direct sources of heat or cold).
Materials also need to be regularly tested to ensure that they are absent from filth, microorganisms and adulterants.
There are further requirements in place for water, colorants and prohibited and restricted ingredients.
Read more about how to adopt a location naming system for your handmade inventory »
Production
The production process itself needs to be documented and recorded when it occurs. This includes provisions such as:
-
The selection, weighing and measuring of raw materials and finished products are reviewed. This is ideally by a second staff member, however for sole proprietors this could be covered by recording two measurements.
-
The theoretical yield for a production batch is compared with the actual yield
-
Uniformity and integrity of the production batch is controlled via reliable processes. This can be things like ensuring that measuring containers are filled correctly and accurately each time and any mixing stages are fully completed.
-
Appropriate measures are taken during the complete process to ensure that contamination does not occur. This is covered in the above sections in detail.
-
Packaging and handling of packaging materials that are likely to come into direct contact with the product need to be contaminant free
-
Final product packaging needs to clearly display information about the manufacture that can be used to trace back to original manufactures. Lot numbers and dates of manufacture are commonly used for this purpose.
Read more: Why is traceability important for DTC makers?
Laboratory Controls
This is to ensure that your testing process adequately allows you to identify issues in your production process. Although this sounds like it is achievable only in a large factory setting there are still a number of important processes to follow in this section.
Read our article on how you can claim for the costs of CPSC testing your products »
-
Your raw materials, including water need to be regularly tested for compliance with specification. If you have purchased your materials, it is your responsibility to ensure that they are compliant and have been fully tested by the vendor.
-
Your finished products need to be tested for compliance with any applicable specifications. This will depend on where you sell and what you make. You’ll want to ensure that any samples you take are fully representative of the lot: this can usually be achieved by firstly standardising your production process as above.
-
Your testing should also factor in any preservation qualities: for example, you’ll want to ensure that your product can prevent microbial contamination under reasonable conditions of storage and use.
-
Samples of raw materials and products should be retained for adequate time periods and are stored in optimal conditions (to avoid contamination)
-
Returned products are regularly inspected and examined for compliance with specifications.
Internal Audit procedures and Complaints, Adverse Events, and Recalls are also covered in detail in the FDA’s documentation, however we will not cover these as they are beyond the scope of this blog post.
Using software to handle your GMP obligations
The most important aspects of GMP for a handmade seller are documentation and traceability.
Craftybase is an MRP system designed for small manufacturers, and was built with these concepts in mind: every aspect of your production process can be recorded, from raw materials used to packaging and shipping. This allows you to track your costs and maintain full transparency and traceability of your products.
Signup for a free 14 day trial to see how Craftybase can help your business.